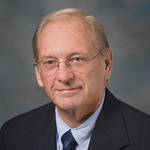
Chapter 10: The Alkek Hospital and the MD Anderson Way of Constructing Buildings
Files
Loading...
Description
Mr. Daigneau begins this segment with two examples of lessons learned from the Three-Building Plan. The first came from Alkek Hospital. The third floor was to house all the diagnostic imaging equipment, but by the time construction reached the third floor, the technology had changed and the most up-to-date equipment would not fit in the rooms. They had to tear out everything and redesign the rooms. The second example involves problems with moving users into new buildings. Mr. Daigneau summarizes the goal that he set for MD Anderson building projects: three years from the statement "I want a building" to moving in. Because "time is your enemy," his strategy was to reduce construction time as much as possible and to delay building out shells to the last moment (providing opportunities for needed design changes). He describes how this works and also sketches other strategies that preserve options in building projects: how to work with architects, how to use the design-build system to an advantage, types of designs to focus on. He notes that he and others studied how malls are built to exploit ideas about preserving flexibility. Mr. Daigneau notes that he took pride in the fact that MD Anderson could build faster than anyone in the Texas Medical Center, including private institutions. He describes the MD Anderson way of building: build fast, don't make mistakes, and engage everyone who will occupy the building all the way through the process.
Identifier
DaigneauW_01_20131003_C10
Publication Date
10-3-2013
Publisher
The Making Cancer History® Voices Oral History Collection, The University of Texas MD Anderson Cancer Center
City
Houston, Texas
Interview Session
Topics Covered
The University of Texas MD Anderson Cancer Center Building the Institution; The Administrator; MD Anderson History; MD Anderson Past; Institutional Processes; Discovery and Success; Building/Transforming the Institution; Growth and/or Change; Obstacles, Challenges; Professional Practice; The Professional at Work; Understanding the Institution; On the Nature of Institutions; Technology and R&D
Creative Commons License
This work is licensed under a Creative Commons Attribution-Noncommercial-No Derivative Works 3.0 License.
Disciplines
History of Science, Technology, and Medicine | Oncology | Oral History
Transcript
Tacey A. Rosolowski, Ph.D:
Were there any other issues that you wanted to talk about with that Three-Building Plan before we go on and talk about maybe the master plan, how that evolved?
William Daigneau, MBA:
Well, there were two things that experiences out of the" primarily the Alkek. The other two buildings were pretty straightforward, but Alkek gave me two lasting impressions about what not to do. That formed the basis of how we approached building in the future. And both these really had to do with time. When we got to the point of actually building out, the third floor was all diagnostic imaging equipment" MRs, nuclear medicine, things like that. So by the time we got to" we were starting to build out the third floor. We were putting in the ductwork for the heating and ventilation system. And this is how I got to know Dr. Murphy pretty well, by the way.
Tacey A. Rosolowski, Ph.D:
And this is William Murphy, just for the sake of the recorder.
William Daigneau, MBA:
Yes. So all of a sudden, at one of these meetings, Mary Ann Newman says" core team meetings" says, Well, Diagnostic Imaging wants to put in the latest model MR." Well, fine. Do we have it in the budget?" Yeah, we can cover the cost of the machine, but there's one problem." What's that?" They won't fit in the rooms that we designed for them." What?" So to make a long story short, of course I went to see Dr. Murphy. I said, Do you understand the problem here?" He said, Well, I don't know what to do, Bill. This is the latest technology. If we put in the older-style machines" you know" this is the best we can offer. Why would we open a brand-new hospital and put in the older-technology machines in it?" Good argument, Dr. Murphy. I'll see what we can do." So we ended up tearing out everything we had built on the third floor. It was all throwaway construction. All that shiny ductwork above the ceilings, brand new, ripped out and put in a dumpster. Redesigned the whole floor to accommodate the new machines. Second incident was we're getting ready to move in. By the way, we hired" I didn't trust anybody there yet, so I argued successfully that we're going to hire a move manager, somebody from the outside that does nothing but manage the moves into new hospitals. That's all they do. That's what their career is. We're not learning at the school of hard knocks. We're going to meet this deadline, hire a move manager. We never used a move manager again in that context. But we hired this guy, and used his system basically as a blueprint to create our own. But we're getting ready to move in and starting to train the nurses on the floor, and the nurse call system" well, how does this work? What do you mean how does the nurse call system work? To make a long story short, we had this very modern, technological nurse call system, but they still wanted the lights above the room. You know, so he hits a button and it glows red. It says, oh, patient in room" which was old technology. So that taught me about technology transfer. You can't just buy the technology and then tell people, Well, we've got this brand-new system. Go for it." These nurses were brought up under an old technology, an old system. So technology was moving at a speed faster, in some cases, than some people could accommodate it and faster than some buildings could accommodate it. So what's the solution? Because it takes you three years, at minimum, to go from I'd like to have a building to let's move into it. During that three-year time period, technology is marching forward constantly. So if you design that building for a certain technology, by the time you move into it, that technology may be out of date. Or vice versa, that technology may be of a kind that the people who are going to use the building are unfamiliar with because it reshapes practice or whatever. So what's the lesson here? Time is not your friend; time is your enemy. So what's the solution to deal with this? Well" which were two innovations at Anderson, which kept me on the public speaking circuit for a while. Number one is to reduce the time of construction as dramatically as you can. In other words, if it normally takes" by the way, the time from Dr. LeMaistre saying, Let's build a new hospital," to the time we actually moved into the hospital was almost eight years. So the one solution is to build as fast as you can and compress" you know" if it takes eight years, you want to compress that by half to a third" or to two-thirds. So you want to go down to four years" between four and six years, depending on how complex the building is. If that's normally what it took you, eight years, because technology changed so much in eight years that that new building will no longer be new by the time you get it done. So compress that time to construction. The second thing that we innovated on was the last possible moment, or what I call just-in-time construction." And that is to delay anything you can in build out to the last possible moment. So a number of things evolved from that. First of all, as large a floor plate" or as open a floor plate as you can build unrestricted by columns and cores, to have a construction approach that allows you to make decisions as late as possible on critical" especially technology decisions. Things that are low technology, like waiting rooms, who cares? But any OR suites, MR suites, anything that uses technology, delay as possible. Build as many channels or paths between floors as you can to accommodate new technology" new wiring. Whatever you designed it for is not going to be enough in the future, so how are we going to try to power up this thing in the future? How are we going to get to it? So a number of principles became laid out about how we would build at Anderson that we applied building after building after building and dictated our approach to building construction, the use of the core team, decision making, plan reviews. Everything was designed to compress the construction schedule as much as possible and to build at the last possible moment.
Tacey A. Rosolowski, Ph.D:
What are the strategies you used to speed up construction? I'm just having a hard time getting my head around that one.
William Daigneau, MBA:
So up until Anderson did it and the law had been changed, nobody had used design-build except on a couple of dormitories" very simple buildings. Design-build offers you the opportunity to have" normally, under the old process, you'd have to have your design and specifications 100% complete so you could bid them. Under design-build, since the person in charge of the" you know" the company running the project managed the architect, he or she could say to the architect, I want the foundations and structural plans completed first because I want to bid them right away. After that's done, then you can work on the finishes and the mechanicals and other things, but right now I need the excavation plan, foundation plans, and structural plans now. And while you're finishing off the design, I'll start construction." So it allows you to fast track the construction by managing the completion of the design to match your sequence of construction, so it shortens the time to construct.
Tacey A. Rosolowski, Ph.D:
I imagine that also means that there began to be a number of architects who knew how to work with that system.
William Daigneau, MBA:
Yeah. Well, the other approach is construction management, and there the owner basically tells the" so what we would do is negotiate contracts with the architect. Even though we had the architect under contract ourselves and the construction manager running construction, we'd have the construction manager run up his whole schedule and set dates for when he needed various designs completed. Then we'd go back to the architect and tell the architect, Your contract is based on four phases" five phases" and you need to complete these documents by this date, by that date, by that date." So we would manage that part of it ourselves, but all the design basically to compress all of the construction schedule by allowing us to begin construction before all plans and designs are completed. So okay, how do you do that? That led us to, well, the only way you can really do it is keep that floor plate as open as possible, because we won't actually get to the interior partitions until later on, so we don't want to design something in the way of laying out exam rooms, offices, whatever. So the only way to do that is minimize the number of columns. So we studied other industries and how they did that. I used to, in my presentations, talk about where we learned this stuff from. Well, one thing is we learned about what was called the mall developer." So how do mall developers build malls? Well, the first thing they do is they determine what the capacity of the land is, how big it is, and how big of a mall they can build. Well, once they have that determined" which is the master planning phase, by the way" once they determine that, then they look for, well, I can accommodate four big boxes" what's called anchors. I can accommodate, on this land, four anchor stores. So they go out and they try to find the anchors right away because anchors have" you know" Target has a certain way they build their stores. Macy's likes this. So they get the anchor stores under commitment and their designs started. If you look at a mall, they start building the biggest stores first. Then everything in between the stores" all the other outlets" are built last, and they're built basically so you can divide them into 2,000 square foot, 4,000 square foot, 6,000. So Gap comes and says, Well, I want to be between Macy's and Dillard's, but I need 6,000 square foot."
Tacey A. Rosolowski, Ph.D:
Oh, so you can" ?
William Daigneau, MBA:
Well, you can move that wall anywhere. Now, they may only leave 2,000, but then another retailer comes and says, I only need 2,000, but I want to be next to Dillard's." Okay, there you go." So that's how a mall developer does it. So we started applying the same principle. We created what was called kit-of-parts. If you have a column spacing of thirty-five foot or thirty-three foot, you can fit three exam rooms in between those columns, two conference rooms, and one MR suite. Everything fits in that spacing. So we were able to tell the architects early on we want a building with thirty-three-and-a-half feet between column spaces. Tell the structural engineer to design floor slab to accommodate that. Because we knew once that floor plate was done, we could fit all these combinations in there. So we compressed it. We went to standard floor plates, wide open as much as possible, pathways between floors for future, in case we missed something. And that happened in IT. IT kept wanting larger cable size all the time. Well, that was the old technology. We need this technology." But that was your standard." That was our standard last year. Our standard this year is this." I mean, that's how fast it would change.
Tacey A. Rosolowski, Ph.D:
Sure. And nobody was anticipating that" no one.
William Daigneau, MBA:
So we had pathways, we had floor plates, and we had a procedure that could build fast to the point that I always" I took some" for our team, some pride in the fact that I was told once that as a public institution, we could build faster than anyone else in the Texas Medical Center, even the private ones.
Tacey A. Rosolowski, Ph.D:
Wow.
William Daigneau, MBA:
It became a joke. Well, we don't build as fast as you do." I mean, you'd get these comments because" both inside the industry and just casual observers" you know" " How can you get this underway so quickly?" Now, I told you about people. To build fast like that and not make big mistakes, you have to have pretty good information flow constantly, not only amongst your construction team but with the users. So that approach only works if you can engage the people who are actually going to occupy the space all the way through because you're making decisions on a daily basis that are paced with the construction of the building. So you don't have to pick colors out yet. We'll get to colors. We don't have to worry about floor finishes yet, but I need to know the room dimensions. So you need to have very strong working relationships with, like, Radiation Oncology, Diagnostic Imaging, Surgery" you know" because those are all highly specialized spaces that only the people who actually do that stuff understand the details of.
Tacey A. Rosolowski, Ph.D:
Now, am I correct in assuming that for the Three-Building Plan you were not able to have good communication with users?
William Daigneau, MBA:
No. It was one of the criticisms of that project.
Recommended Citation
Daigneau, William and Rosolowski, Tacey A. PhD, "Chapter 10: The Alkek Hospital and the MD Anderson Way of Constructing Buildings" (2013). Interview Chapters. 133.
https://openworks.mdanderson.org/mchv_interviewchapters/133
Conditions Governing Access
Open
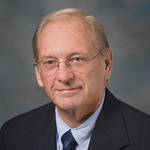